Automated Ingredient Sifting, Feeding & Conveying for Food Manufacturing
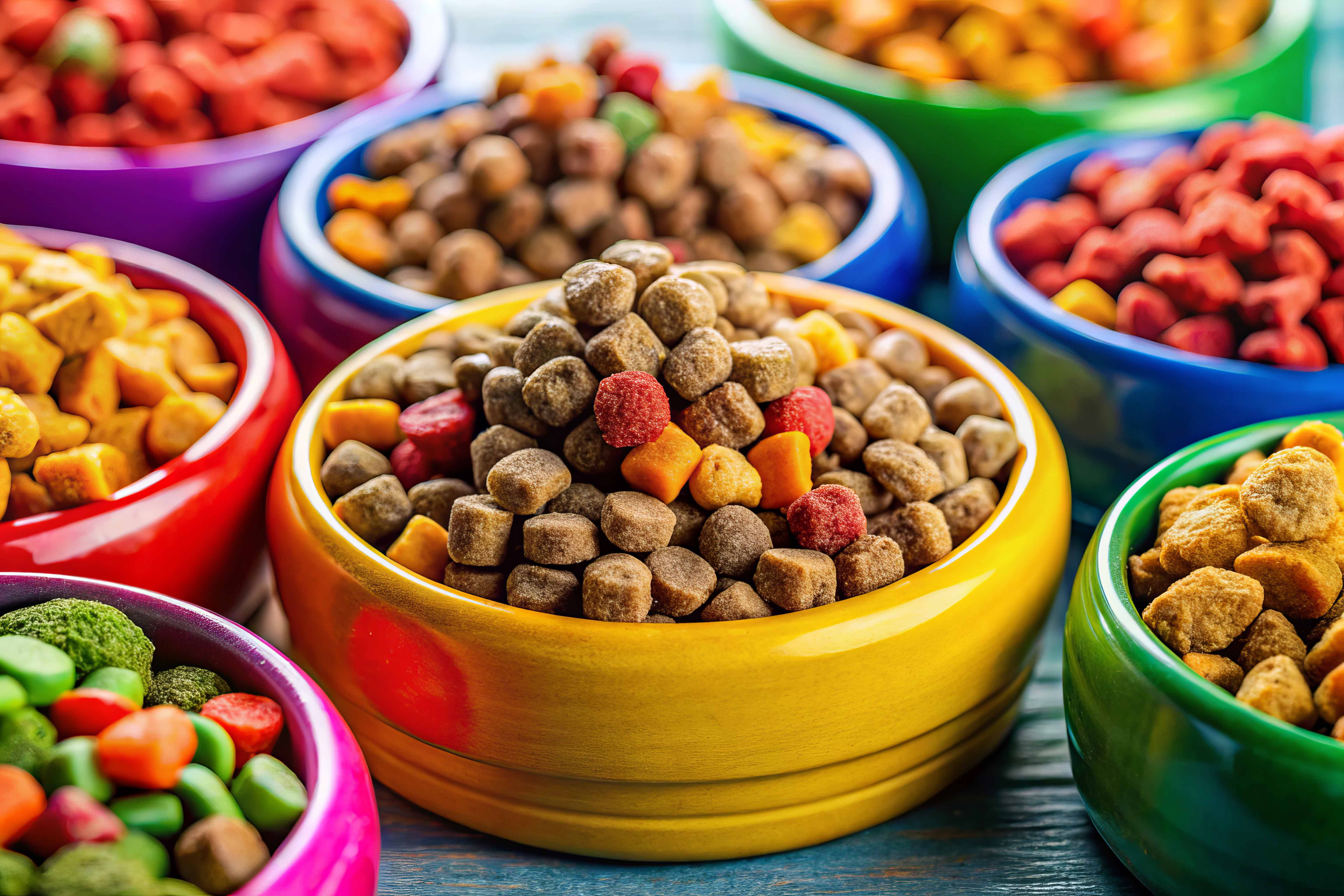
Overview
In the dynamic world of food manufacturing, ensuring product integrity and efficiency is paramount. One of our recent projects tackled the challenges of ingredient handling with an innovative automation solution tailored to the food industry. This case study highlights how we achieved zero cross-contamination and dust-free transfer of ingredients, ensuring precise ingredient addition and enhancing operational efficiency.
Industry Context
Industry: Food
Project Duration: 6 months
Customer Requirements
- Zero Cross-Contamination: Prevent mixing of different ingredients to maintain quality.
- Dust-Free Transfer: Ensure clean and safe handling of ingredients.
- Food-Grade Construction: Meet stringent industry standards for hygiene.
- Precise Ingredient Addition: Guarantee accurate addition into the Weighing Hopper.
- Water Addition Option: Incorporate precise water measurements into the mixer.
Cybernetik Solution
Our solution integrates cutting-edge technology and seamless automation to meet these stringent requirements:
- Dedicated Bag Tipping Stations and Vibro Sifter: Each ingredient is processed individually, ensuring zero cross-contamination by loading only one Silo at a time.
- Pneumatic Conveying System: Facilitates a dust-free environment, critical for maintaining a clean production area.
- Hygienic, GMP-Compliant Design: Adheres to the highest standards in food safety, ensuring both quality and compliance.
- Efficient Operations: The simple and fast operation minimizes downtime, maximizing throughput.
- Systematic Ingredient Handling: An agitator feeds the Screw Conveyor, preventing blockages and ensuring smooth transitions from Silo to Weighing Hopper.
- Precision Checked by Load Cells: These ensure that each ingredient is added in the correct quantities, maintaining consistency and quality.
- Controlled Material Flow: Knife Gate Valve and Diverter Valve manage the flow of materials smoothly and efficiently.
- Water Addition Capability: Enables precise water incorporation in the mixing process, supporting recipe accuracy.
Project Scope
The comprehensive setup includes:
- 4 x Bag Tipping Station with Vibro Sifter
- 4 x Pneumatic Conveying System
- 4 x Storage Silo
- 4 x Agitator
- 4 x Screw Conveyor
- 1 x Weighing Hopper
- 1 x Load Cell
- 1 x Knife Gate Valve
- 1 x Diverter Valve
Conclusion
This project showcases how advanced automation and precise ingredient management can revolutionize food manufacturing processes, aligning with industry demands for safety, efficiency, and quality.
For those interested in seeing the solution in action, we invite you to watch our project video demonstration to gain a full understanding of its capabilities.
Explore how our solutions can transform your operations, providing unmatched benefits in precision and productivity.