Biomass Conveying Solution
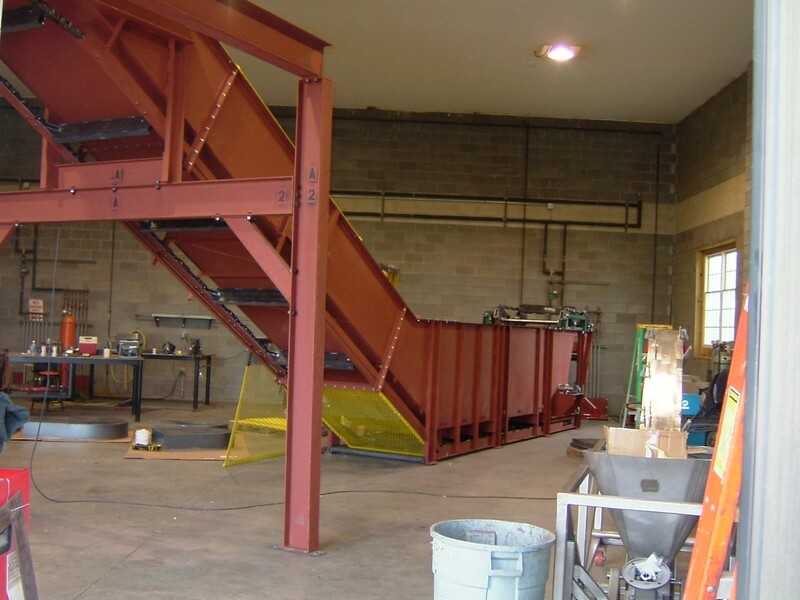
"This Solution has been Operating 12 years 24/7 Without Issues. "
A university campus power plant converted its fuel from coal to wood product biomass. The biomass consists of various chunks and chips with a large portion of fine particle wood flour. When the biomass is received at the plant, it is conveyed to the drying process on an inclined (45-degree), pocketed and cleated belt conveyor at a constant speed. The belt conveyor design turned out to create more problems than it did solutions. The two main issues were housekeeping and control, which are both due to a poorly chosen technology. The result was too much variation flowing to the dryer, and the finer particle biomass would tend to flow back and spill over, creating piles of product at the conveyor inlet and sides.
Having fine particles of wood dust/flour build up outside the process equipment is a serious safety concern as it can be considered explosive under the right conditions. Addressing this safety issue is priority number one. Having to constantly clean up the spillage was a frustrating task. Ensuring a consistent product feed to the dryer needs to be addressed as well.
Powder Process Group consulted with Thomas and Muller and determined that a properly designed screw conveyor would ensure containment and prevent unnecessary housekeeping, eliminate the explosive concern, and convey consistent product.
The solution consisted of a nine-inch-diameter screw conveyor that was fifteen feet long and at a 45-degree incline. Due to the flow function of product, the conveyor requires a force-feeding screw feeder discharging perpendicular into the conveyor via coping interface. The conveyor flights were manufactured from AR-400 to mitigate wear from abrasion. Because the received biomass product was not very consistent either, a variable frequency drive was installed to control the mass flow rate. There are no intermediate support bearings, which eliminates potential for spark and frustrating maintenance.
This solution has been operating twelve years 24/7 without issues.